The Golden Threads of Tradition: An overview of the Sualkuchi silk industry of Assam
Noesis Literary (ISSN: 3048-4693) Volume 1 Issue 1 (Jan - Jun) 2024; pp 71 - 87
The Golden Threads of Tradition: An overview of the Sualkuchi silk industry of Assam
Dr. Nazneen Akhtar
Assistant Professor,
Department of Geography,
Nowgong Girls’ College, Nagaon, Assam
1.Introduction
Handloom weaving is an important aspect of India's socio-cultural legacy, and many states of the country have received international praise for their distinctive features and unique skill. This is likewise true for the state of Assam. The artisans who live in the countryside are greatly influenced by various elements of their surroundings, as well as the various myths, legends, customs, rituals, traditions, ceremonies, social organizations, and so on, which are beautifully reflected upon their textile traditions in one way or another. Furthermore, Assam's geographic position and climate have resulted in the formation of ecological niches for unique and unusual species of silk producing insects. Crucial to the survival and flourishing of these insects are the specific plants that naturally grow in abundance in the state providing food and shelter to these sensitive silkworms (Chakravarty, 2009).
Sericulture has been a successful means of providing gainful employment in rural Assam, and it has huge potential in terms of developing the region's rural economy. It is also significant in the context of helping to create a humanized environment with green cover in the face of global ecological degradation. This ancient cottage enterprise has its roots in Assamese culture and way of life (Phukan & Chowdhury, 2006). And the one industry in which she has global monopoly power is muga silk manufacture. Muga silk is golden in colour with glossy texture. The shimmering appearance of silk is due to the triangular prism-like cross sectional structure which allows silk cloth to refract incoming light at different angles, thus producing colors. In order to get 1 kg. of Muga silk yarn, 5000 good qualities muga and to rear 5000 muga silk worm 104 kg of som and soalu leaves are required. In the year 2014-2015, India produced 158 tones of muga silk out of which 136 tones were produced only in Assam (Gogoi et.al, 2017). Assam is where all of India's muga silk manufacturing began, giving Assam silk a special place on the map of sericulture. Assam also produces mulberry silk, known locally as "paat silk" or "Nuni paat," although not in sufficient quantities to meet demand. Although Assam silk refers to all three types of silk (paat silk, eri silk, and muga silk), the majority of mulberry silk used in Assam is obtained from Karnataka or China due to the qualitative benefits over locally produced paat silk. Although Assam is India's fifth largest producer of mulberry (paat) silk, it faces competition not just from within the country but also from abroad. Furthermore, an infusion of cheaper Chinese silk has led in a continuous reduction in market demand for mulberry silk (Goswami, 2005).
1.1 Weaving pockets in the state
In general, natural fabric production involves three distinct stages: (i) worm rearing and cocoon creation, (ii) spinning, and (iii) weaving. Many Assamese regional pockets have developed competence in these three components for various fabrics. This specialization, on the other hand, may be attributed to the skills, knowledge, and tradition indigenous to a specific place that have been passed down from generation to generation. Furthermore, the environmental adaptability of a location has played a significant influence in such region-specific concentration.
Besides, there are three sorts of weaving establishments in Assam: (i) those consisting of amateur weavers who make cloth merely to cover the needs of the family, i.e. on a subsistence basis. Such weaving takes place in Assam's muga-growing regions, including Sibsagar, Jorhat, North Lakhimpur, Golaghat, and others. ; (ii) those consisting of professional weavers who produce cloth for profit.That is, they weave for their families while also selling their surplus items; such workers are typically part-time. In the lower Assam districts of Kamrup and Goalpara, mostly female weavers weave this type of silk cloth, and (iii) those who are purely commercial weavers who work full-time either individually or collectively under cooperative societies and factories. Such weaving is concentrated in Palashbari and Sualkuchi in Kamrup district, as well as in a few pockets throughout Upper Assam.
Though eri silk production in Assam has improved in recent years, the case of muga silk is not in a very healthy state in terms of the number of villages and families involved, the acreage under som and soalu plantations, or the production of muga yarn. Silk is a lustrous fiber whose popularity grows year after year. However, in the absence of an appropriate strategy and a focused approach, production of all types of silk, particularly muga, is declining in India's eastern region.
The objectives of the paper include the following:
i)To provide an overview of the status of silk industry in Assam with special reference to Sualkuchi silk industry.
ii)To deal with a brief historical analysis of the origin of silk weaving industry at Sualkuchi, and explore the continuity of this age-old tradition till date.
The significance of the present study lies in the fact that it attempts to document the legacy of this household weaving industry of Assam which has brought much glory and fame not only to our state but also our county at large.
2. Materials and Methods
2.1 Study Area
The study is conducted in the Sualkuchi Development Block of the Kamrup district of Assam. About 35 kms from Guwahati, Sualkuchi has a population of 70,962 (2011 census) with 16,975 handlooms and 19,530 weavers. There are eight Gram Panchayats in Sualkuchi block, in all of which, weaving is a dominant occupation. Sualkuchi is located at 26.17°N lat. 91.57°E long. (Fig. 1) and has an average elevation of 35 m (115 ft).
Fig. 1 Location of the study area
2.2 Data collection and Methodology
The study is basically exploratory and qualitative in nature. Data was gathered using two methods: primary data collection and desk research. Focused group discussions (FGD), strategic interviews, and questionnaire surveys have been administered to the different participants in this study area. Conversations have also taken place with representatives and other stakeholders who are engaged in marketing handloom goods, etc., to both domestic and international consumers, as well as providing inputs to the handloom industry.
The secondary data was gathered through desk approaches, which involved gathering data from both published and unpublished sources, including books, research journals, project reports, published theses, magazines, newspaper articles, online sources, government documents, census reports, and more from organizations like the Central Silk Board, Khanapara, Guwahati; the Department of Handloom & Textile; the Directorate of Sericulture and Directorate of Economics and Statistics (Govt. of Assam); and the Regional Silk Technological Research Station.
A total of 451 households from the 3967 total households in the study area—which includes 3 Gaon Panchayats and 4 villages where more than 50% of the households are employed in weaving—were chosen through the use of purposive sampling. The technique used is purposive in the sense that samples (only those villages have been considered where weaving is a full-time occupation) have been chosen in accordance with the objectives of the study. In light of this, four villages—Bathangaon and Srihati from Paschim Sualkuchi G.P., Sualkuchi village from Madhya Sualkuchi G.P., and Bamundi from Pub Sualkuchi G.P.—that represent 5–15 percent of all households have been purposefully chosen and surveyed. The people in the remaining villages have given up weaving as a career and switched to other sources of income.
3. Results and discussion
3.1 The silk industry at Sualkuchi: A retrospect
"Every woman of Assam is a born weaver, who can compose fairly dreams in their weaves," Mahatma Gandhi said when he visited Sualkuchi and saw the woven fabrics.
Sualkuchi is a census town in Assam, India, made up of two revenue villages: Sualkuchi and Bamundi. Sualkuchi is located in the Kamrup district of Assam, about 35 kilometers from Guwahati, the state capital. Over the years, Sualkuchi has grown as a Development Block with 16 villages, viz. Sualkuchi, Bongsor, Barlah, Saupara, Bathan, Srihati, Gandhmou, Sarulah, Kaeyatol, Bamundi, Halogaon, Siliguri, Hardia, Tokradia, Sobangsah and Ramdia. Sualkuchi is known as the 'Manchester of the East' because it is the busiest Silk Textile center in India's north-eastern region. It is also the world's largest muga weaving cluster. This is the home of the Assamese Baishyas, whose primary occupation has always been silk processing and weaving.
The exact date of the introduction of silk manufacturing in Assam or the Sualkuchi silk weaving tradition cannot be determined. However, historical records show that the katonis, or rearers of paat silk arrived in Assam in the 12th century AD (Bhattacharjee, 2014). Sericulture was actively practiced in the current district of Kamrup in Assam, as documented in Arthashastra, Harshacharit, and other texts. In 140 B.C., sericulture most likely spread to India from China, primarily into the valleys of the Brahmaputra and the Ganga. It is, however, difficult to pinpoint the exact period of muga sericulture in Assam (Chakravarty, 2009). Sualkuchi's history can be traced back to the days of Kautilya. According to Kautilya's Arthashastra, in ancient Kamrup, there was a principality known as Suvarnakudya, which was famous for its silk industry. Among the silk fabrics he mentions are Vonga's Dukula, Khauma, and Patrorna, Kashi, Pundra, Magadha, and Suvarnakudya, and China's Kauseya. K.L. Barua, for example, has interpreted Dukula as muga, Khauma as eri, and Patrorna as paat silk (Baishya, 2005). Suvarnakudya was known for its silk industry, so there must have been a Tantubaya or Tanti community, as well as traders or Mudois in fabrics. However, in modern Sonkudiha, there is no trace of the Tanti or Mudoi communities, whereas Sualkuchi still has these communities.In fact, whatever the origins of Sualkuchi may be, its history can be traced back to the early 17th century. Swarnakuchi may be a dialectical variation of Soalkuchi/ Sualkuchi, and Swarnakuchi may be a variation of Kautilya's Arthashastra, as Manchester of England is from the Roman name Mancunium (Mantoux, 1948).
The Ahom reign saw significant progress in Sualkuchi's handloom sector, which could not have occurred during the British regime in India. This was due to the rulers' personal concern and interest in the silk industry. Sibsagar, the capital of the Ahom kingdom, became a hub for various types of silk, and fabrics made from eri, muga, and paat have since become Assamese folk dress. During the reign of the Ahom dynasty (1228-1826), spinning and weaving became popular and indispensable occupations.
Swargadeo Pratap Singha's minister Momai Tamuli Barbarua made it mandatory for every male member of the society to make a bamboo basket and every female member to spin a certain quality of yarn during his reign (1603-1641). The necessary steps were also taken to settle the professional community and assign them to different 'castes'. Weavers from other parts were thus organized and settled at Sualkuchi in the district of Kamrup. This could be one of the main reasons for the concentration of professional weavers in Sualkuchi (Das, 2008). Mohammedan experts in embroidery work were brought from Delhi and established in Assam during the reign of King Jayadhvaja Singha (1648-1663), encouraging Assamese people to learn the art of embroidery for the upliftment of indigenous crafts in Assam (Gait, 1982). Swargadeo Rudra Singha, the Ahom king who ruled from 1696 to 1714, took the initiative to maintain a weaving department and skilled weavers to supply the royal wardrobe with a variety of cloth. These royal looms were known as 'Rajagharia looms,' and they were operated by expert female weavers from all over Assam. In exchange, they were given free land and other benefits. Through his envoys, King Rudra Singha also brought new ideas, techniques, and designs for the art of weaving from various parts of India and encouraged Assamese weavers to implement those ideas. The encouragement provided by the Ahom kings boosted Assam's silk industry (Phukan, 2012).
Under the Ahoms, the production of silk cloth was extended to all sections of the valley, including the upper castes. Queen Sarveswari, the wife of Siva Singha (1714-44) is said to have encouraged the ladies to spin and weave and to have imported designs and patterns from other parts of India (Bhuyan, 1985). Perhaps it was at this point that weaving became a part of everyday life for Assamese women. No woman was considered accomplished unless she had mastered the art of weaving. Female labor was thus given a mandatory character, which was advantageous in many ways. On the one hand, it assisted thousands in meeting their cloth requirements as well as the state demand; on the other hand, it assisted in keeping a sufficient quantity of cloth of various varieties in the royal store for presentation to foreign courts and dignitaries (Bhattacharjee, 2014). Thus, the arrival of the Ahoms provides a clearer picture of the importance of silk weaving in the state of Assam, among Assamese rural folk, and the role of women in it.
The true test of the silk industry's tenacity began with the arrival of Britishers in Assam in the early nineteenth century. Following the Yandabu treaty in 1826, English officials of the East India Company entered Assam and conducted extensive research on the state's economy. Among several works, Francis Hamilton's "An Account of Assam" is noteworthy for containing references to sericulture practice in Assam. According to this account, native women of all castes, from the queen to slave girls, could weave all types of silk, and three-quarters of the population wore these products. The raw material is rarely purchased; instead, each family spins and weaves the silk that it raises (Baishya, 1986).
Sualkuchi's weaving industry was almost entirely confined to the Tanti community of Tantipara (around the current Bazar Chowk) until the 1930s. Sualkuchi had a number of cottage industries up until the 1940s. Aside from the Tantis' handloom industry, some of the cottage industries included oil pressing in the traditional ghani in the Keotpara segment of Bamun- Sualkuchi; goldsmithy in the Sonaripara hamlet, pottery in the Kumarpara hamlet, and silk rearing and reeling occupation of a community in West Sualkuchi. Other industries are nearly extinct, and artisans have taken up silk weaving as a profession.
The Second World War boosted Sualkuchi's weaving industry, with demand for fabrics increasing as prices rose, encouraging 10 to 12 Tanti families to establish weaving factories employing wage weavers. The introduction of the fly shuttle loom by one Kaliram karikar (karikar means an expert artisan) at the suggestion of one English Superintendent was another significant event in technological advancement. Because of this initiative, handloom weaving was moved from a household occupation to a factory-based production. Conservatives were initially opposed to the introduction of the fly shuttle loom, but after a few years, realizing its importance and higher productivity, they replaced the throw shuttle with it, and thus, this improved loom developed by an English "half weaver and half mechanic" John Key in 1733 was introduced in Assam after more than two centuries of its invention.
3.2 Growth of the silk handloom cluster and its survival
The 1970s saw the development of this cluster. The factors that apply to the establishment and development of the Sualkuchi silk industry include: labor availability, raw material availability, and specialization in a particular art. In addition, a lot of migrant weavers have been drawn to it, especially Bodo female weavers from different Assam districts.
For a variety of reasons, this industry did not completely disappear but rather stagnated, in contrast to many others. Above all, it was an indigenous production that was definitely a success. Secondly, there were no equivalent alternatives available for these goods, and there was no need to pay for extra labor. Third, in the last section of the work, the women of one family help their neighbor and are helped in return by their neighbor. After that, weavers could use a single loom process to create a wide range of clothing items, including chadar, mekhela, dhoti, and so forth. This benefit of varied production satisfied the needs of both male and female family members while preserving supply and demand equilibrium (Kalita, 2013).
3.3 The weaving set up in the silk town
The fly-shuttle's rhythmic rattle, "Click-clack, click-clack," draws people's attention as it moves through Sualkuchi's streets from 8 a.m. to 10 p.m., with a lunch break from 12 p.m. to 2 p.m. 75 percent of the households in the area are employed as fly-shuttle loom silk weavers. In Sualkuchi, there is a weaving shed with looms for production in almost every home. These days, weaving is organized here into tiny, entirely commercial courtyard businesses. Sualkuchi is now the state's "Benchmark" for commercial silk weaving, in fact. "Though silk is not uncommon in other parts of Assam, Sualkuchi claims a technique, quality and reputation of its own which is unique so far as paat and muga silk is concerned," the Census of India, 1961 noted in reference to Sualkuchi. The establishment of this industry in Sualkuchi has led to the following benefits for the local population: i) direct and indirect employment; and ii) assistance in meeting the state's and the region's clothing needs (Mahanta & Sonowal, 2000).
3.3.1 The core-cluster actors
The master weavers, independent and dependent weavers, reelers, yarn winders, ancillary workers, yarn suppliers, and traders make up the core cluster actors in Sualkuchi. Sualkuchi's courtyard industries consist of family-owned partnerships or sole proprietorships. These proprietors are referred to as "Mahajans," or master weavers in general. This group was formerly involved in weaving, but these days, they mostly work as loom owners or traders, handling the entire task of receiving orders and seeing them through to completion. They are skilled weavers with a wealth of historical weaving industry knowledge. In addition to managing the entire production line, the Mahajans also handle marketing and finance. Many of them have their own stores or showrooms in Guwahati, the capital city, which is only 35 km from the silk town. Most master/entrepreneur weavers raise the money on their own to set up and operate their looms; they may borrow from friends and family or apply for various types of loans from financial institutions.
A class of wealthy middlemen focused on the silk business has recently arisen in Sualkuchi. There is a class of master weavers who market their goods through middlemen who run retail stores and operate in the process rather than selling their goods directly to consumers. This proves the importance of these middlemen in helping to market the finished silk fabrics. These middlemen are known to stock their goods until the busiest times of the year, which is usually around marriage and Bihu season. At that point, the prices rise significantly and they stand to gain the most.Even though Sualkuchi is home to many master and entrepreneur weavers, there isn't any ruthless rivalry among them, and aside from a brief lean season, Sualkuchi silk products are in high demand practically all year round.
The weavers in Sualkuchi who work under Mahajans are the loom-less weavers. The Mahajan family owns the factories where the weavers labor for over ten hours every day. During business hours, which start at 8 a.m. and end at 10 p.m. with breaks in between, the proprietor serves tea and snacks. In most cases, the Mahajans provide lodging. Weavers receive festival advance during Puja or Bihu. A few Mahajans also occasionally provide bonuses. Nevertheless, the weavers are not eligible for any retirement benefits, such as provident fund, gratuity, etc., or other benefits like insurance, healthcare, paid time off, etc.
The scarcity of labor is one of the serious issues facing the silk industry. Due to the requirement that weavers receive payment in advance of their engagement, many Mahajans are now forced to hold onto one or two extra looms, sometimes even more. This has also prompted a large number of wage weavers from other adjacent regions of the state to come work as hired weavers here. Occasionally, a clever and moral wage worker begins operating one or two looms with the money he has saved up plus an advance from the master weaver, or Mahajan, and eventually rises to the position of master weaver, hiring wage workers. These weavers are classified as independents.
Women weavers make up the majority of the dependent class of weavers. In Sualkuchi, women predominate in the labor force. Young women who are migrant and primarily from nearby tribal communities—Bodo and Rabha women in particular—make up the workforce. They come to Sualkuchi in search of wage work in order to support themselves. Because they are employed as wage, contract, or hired laborers and are subject to abuse at the hands of master weavers, this group of weavers suffers the most. Some of them settle down in Sualkuchi after mastering the finer points of weaving here, while others establish their units after going back to their home villages or to other places. Over 5000 Bodo female weavers from various Assamese districts have come to Sualkuchi because of the comparatively higher wages here.
Together, the ancillary workers, yarn winders, and reelers make up a specialized group that is also a member of the weavers' family. They complete the pre-weaving task, which takes a lot of time and effort. They receive no extra compensation for this work either. Muga reeling is a process called Bhir or Bhowri. The yarn is created in hank form by re-reeling raw silk once more. You can purchase local raw silk in lecchas or hanks. Twisted, bobbined, and warped are necessary pre-loom operations. Using vegetable dyes made from a variety of plant and herb parts, including stem, wood, root, bark, leaf, flower, and fruit, silk yarn can also be commonly dyed using this method.
The suppliers of yarn are also crucial because, although muga yarn is reeled here by purchasing cocoons from Upper Assam, Boko, Garo Hills, etc., paat yarn is purchased from Bangalore, and tassar from Kolkata. In the past, some muga weavers would travel to the Upper Assamese towns of Jorhat, Lakhimpur, Dhakuakhana, and others to gather muga cocoons directly from other weavers. They would then store the cocoons for the year, reel them, and use their looms to weave fabrics. Local traders now collect the cocoons in sacks, transport them in bamboo baskets, and sell them in Sualkuchi, replacing this practice. The handloom industry in Sualkuchi is becoming increasingly reliant on inexpensive Chinese tassar as a raw material due to the lack of muga yarn. Due to its higher tensile strength, the Chinese mulberry has the unsettling potential to penetrate a significant portion of the wrap material market, despite its limited use due to its poor color absorbance. But the muga's natural strength has always been its exquisite touch and appearance—a rare quality that Chinese tassar lacks.
Traders are another important player in the silk industry, in addition to those directly engaged in it, since they play a crucial role in creating connections between weavers and buyers. In addition to other natural silk fabrics, these traders deal in eri-muga silk fabrics. It has been noted that younger generations are highly interested in the silk trade, especially the muga and eri trading ventures. Actually, a few of the traders are also weavers, and they have one or two looms at home that they either use themselves in their spare time or hire other weavers to use. The majority of traders trade both retail and wholesale.
In March 2013, Sualkuchi weavers went on a vandalism rampage to defend their art and means of subsistence against the illegal sale of imported silk masquerading as native silk. The state's renowned handloom industry is under threat because some dishonest traders are importing large quantities of paat fabrics and imitating the intricate designs and motifs that Sualkuchi weavers have perfected. This is a problem for weavers and small-scale handloom entrepreneurs. Local traders and weavers are rapidly losing market share as wholesalers flood local stores with Banarasi silk products. A few traders had given their lovely designs to Banaras artisans who were making products in the Sualkuchi style.
3.3.2 Raw materials used
Sualkuchi weaveers weave majorly pat and muga; a few people weave tassar, but eri is not woven there. A few Sualkuchi traders buy and resell eri goods from the Palashbari/Mirza region. The majority of paat yarn is imported from Bangalore. Muga from Kolkata and tassar from Upper Assam, Boko, Garo Hills, and other areas are purchased here. Sualkuchi, which was previously known for items made of golden muga silk and Assam mulberry yarns, now primarily uses Tassar and Karnataka mulberry yarns. Muga is still utilized, albeit less frequently. Although muga-mulberry and muga-tassar blending has developed, the products' composition is not specified. The product line is restricted to meet local demand, and the primary market for the product is the domestic market. However, the availability of muga cocoons, which is actually decreasing for a variety of reasons, determines the number of muga looms in Sualkuchi.
3.3.3 Loom details and accessories used
The loom and accessories used by weavers have remained remarkably simple. In addition to cotton, silk is woven on the traditional handloom, known locally as taat saal. Drawboy, dobbey, and jacquard looms are used to create intricate patterns on textiles. Dobbeys are used to design the center of the cloth, while Jacquards are used to design the border floral designs. However, only Dobbeys are now used, and floral borders are woven separately within the same chadar or saree and then sewn by the tailors. This is due to the weaver's strenuous physical labor in jacquard weaving. Design experts sketch the designs on graph paper, which is then punched (a technique known as card punching) and fitted to the Dobbey. Overall, weaving is a very laborious process. A mekhela takes about two days to weave, a chadar three to four days, and a saree a week. The wage is determined by the number of floral picks woven into the fabric as well as the overall weaving cost of the fabric. Wages are paid in units, which are shown on the punch card as the number of designs with 100 choices, also known as a unit or Muthi. Other small appliances used in the fabric manufacturing process, in addition to looms and their accessories, include letai, chereki, and ugha, which are primarily made of bamboo.
3.3.4 The production procedure
The entire process of production of silk fabrics in the looms i can be broadly categorised into 3 main parts: the pre-loom, loom and post-loom stage.
The steps involved in the production process are each briefly described below:
1.The first step in the pre-loom process is acquiring raw materials, mainly from Karnataka (paat yarn), Kolkata (tassar yarn), and the Boko and Garo Hills region (cocoons from Jorhat, Sibsagar, Dhakuakhana, etc.) in Upper Assam, where muga is reeled.
2.Only the muga cocoons are reeled here; the other raw materials are purchased as yarn from sources outside the state. "Reeling" or "throwing" refers to the process of unraveling continuous filaments in the form of yarn. Most reeling is done in "cottage basins" and "charkhas," which are essentially nonexistent these days.
3. Spinning is the process of creating a single yarn from the irregular filaments of cocoons. The main tool used to spin cocoons into yarn is the drop spindle (also known as a takuri or takli). Children and women alike mostly engage in spinning as a hobby in their free time.
4. The majority of the time, natural sources are used for dyeing after yarn is obtained. Nonetheless, synthetically colored yarn is now easily accessible in the market.
5. The yarn is wound onto reels or loosened after dying. This is a prelude to the preparation of warp and weft known as winding. Weavers find that winding warp yarn on bobbins is the most acceptable technique.
6. Warping includes winding the warp yarns onto bobbins, which are positioned within a wooden frame known as a reel. These reels' yarns wind around a vertical drum after passing through a reed. Locally, this is referred to as "batikata" or "tattbati." Drum warping, which is more advantageous for commercial use and can be done indoors, is a more recent development.
7. The task of passing the warp through the reed and the healds is the next step, after which the yarn sheet is wound in tension around a beam. We call this beaming.
8. Another ancillary task completed by qualified individuals in the pre-loom phase is card punching. Design experts sketch their ideas on graph paper, punch hard board cards, and then fit them to the Dobbey, a crucial loom accessory for weaving complex patterns and upgrading products.
9. The process of looming is used to properly fit the warp onto the loom and finish any preparations needed for weaving.
10. To create fabrics that match a design, weavers interlace two sets of yarn—warp and weft—at right angles in a predetermined order.
11. The Sualkuchi fabric is cut off the loom to be sold at the post-loom stage. Very little is done in terms of product specifications, labeling, and specially designed packing techniques.
3.3.5 The product line
Weaving traditional fabrics for women's upper and lower bodies, such as mekhela and chadar, blouse pieces, plain pieces, or thans, or plain sheets that can be sewn into mekhelas, shirts, chadars, and other items, is the main activity of the looms in Sualkuchi. Looms are used to weave Jainsem, or traditional women's clothing worn by the Khasis and Jaintias of Meghalaya, and Dhara, in addition to traditional goods for Assamese women. Even though sarees are woven on a small number of looms, this is still a business.
Regarding the preservation of the design, this has also undergone stages of gradual evolution over time, making it an art form in and of itself. According to information gathered in this regard from the Sualkuchi area, simple banana leaves were once used to preserve designs. The thick sheath of the areca palm tree took the place of the banana tree's less durable leaves. The indigenous weavers created yet another technique, though, by weaving the designs on coarse fabric or net-like cloth, in response to the limitations placed on the preservation of designs even on the leaves of the areca palm tree. The indigenous weavers created yet another technique, though, by weaving the designs on coarse fabric or net-like cloth, in response to the limitations placed on the preservation of designs even on the leaves of the areca palm tree. These days, skilled and trained weavers are also becoming more and more popular in their use of graph paper and other computer techniques with appropriate software. The way that weavers preserve their designs indicates that traditional designs in rural areas are stored in design scraps, but the issue of their untimely demise is a serious concern.
The use of environmentally friendly natural dyes on cotton, wool, silk, jute, and other textiles is becoming more and more popular worldwide as people become more conscious of the need to maintain a healthy and sustainable environment. Because these natural dyes are biodegradable, non-toxic, and not carcinogenic in the wild, they are safe. The Sualkuchi people are also aware of the harm that synthetic dye use causes to the environment. As a result, environmentally friendly products are increasingly valued highly these days. But regrettably, the influx of artificial products is negatively affecting our traditional roots in one way or another as a result of growing commercialization and a broader impact of globalization processes.
The changes that were adopted by modern sericulturists, albeit at the expense of traditional practices, have undoubtedly led to a greater efficiency in silk production and consequently the quantity of silk reaching the market is likely to increase. However, there is much more to be done in this sector, at research level as well as at the government level so as to take silk culture and hence silk production to greater heights (Narzary, et al. 2023).
4.Conclusion
Sualkuchi is a weaver’s paradise in the state of Assam. This study is a valuable addition to the existing literature on the heritage of the industry and skills of the Sualkuchi weavers. Since the beginning of time, Assam and Sualkuchi in particular have carved out a unique place for themselves in the global silk production industry thanks to geographical advantages like easy access to raw materials, skilled labor, and a specialization in weaving. But since globalization, this industry's state has changed from what it was before. Even though silk production and income are trending downward, there is still room for growth because of the increasing demand for silk on the international market. To keep the impoverished at the margins, the government must take action. Above all, programs and policies must be used in concert to help the Sualkuchi weaver communities develop genuine adaptive capacity.
References
Baishya, P. The Role of Small Scale and Cottage Industries: A Case Study in Kamrup District of Assam. 1986.
Baishya, P. The Silk Industry of Assam. Spectrum Publications, 2005.
Bhattacharjee, M. Silken Hues, Muted Voices : Women in the Silk Industry of Assam. DVS Publishers, 2014.
Chakravarty, R. Assam Silk. Edited by H. Deka and Assam: Land, Thomson Press, 2009, pp. 187–191.
Das, R. Marketing Problems of Handloom Products: A Micro-Level Study on Sualkuchi Village, the Prominent Silk Weaving Centre of Assam. 2008.
Gait, E. A. History of Assam. Guwahati: LBS Publications. 1982.
Gogoi, M., Anumoni Gogoi, and Bulbul Baruah. "Exotic muga silk: pride of Assam." International Journal of Applied Home Science vol. 4 no.1, 2017, pp. 72-78.
Goswami, P. Indigeneous Industries of Assam: Retrospect and Prospect. Anshah Publishing House, 2005.
Kalita, R. ‘An Introduction to the Sericulture Industry of India as a Means of Livelihood’. Review of Research, vol. 3, no. 1, 2013.
Mahanta, N., and D. K. Sonowal. ‘Market Economy and Marginalisation of Women: An Exploratory Study of Women Weavers’. Globalisation, Culture and Women’s Development. Jaipur And, edited by R. M. Sethi, Rawat Publications, 2000.
Mantoux, Paul. The Industrial Revolution in the Eighteenth Century. Routledge, 2015.
Phukan, R. ‘Handloom Weaving in Assam:Problems and Prospects’. Global Journal of Human Social Science, vol. 12, no. 8, 2012, pp. 17–22.
Narzary, P. R., S. Manimegalai, R. Shanmugam, B. Vinothkumar, A. Suganthi, and P. Radha. "Golden Threads of Tradition: The Endurance And Evolution of Muga Culture And Silk Weaving in Assam." Journal of Survey in Fisheries Sciences , Vol. 10, no. 3, 2023, pp. 63-70.
********
Author's bio: Dr. Nazneen Akhtar is currently working as an Assistant Professor in the Department of Geography, Nowgong Girls’ College, Nagaon, Assam. She is a Gold Medallist in Geography from Aligarh Muslim University and has done her PhD from NEHU, Shillong. Her research interests include livelihood, rural geography, women-centric issues, human ecology etc. She resides at Hatigaon, Guwahati.
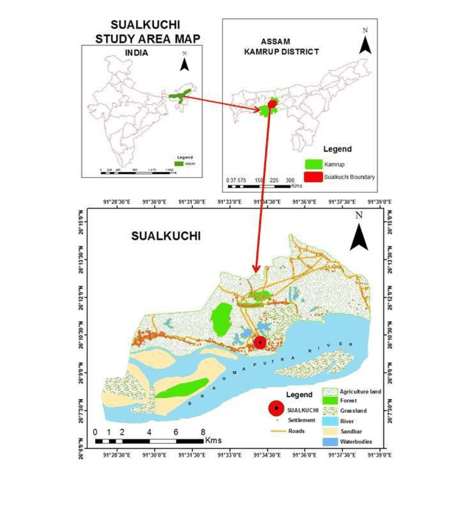
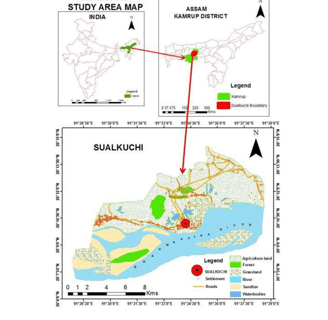